How to Start Your First Guitar Pedal Building Project
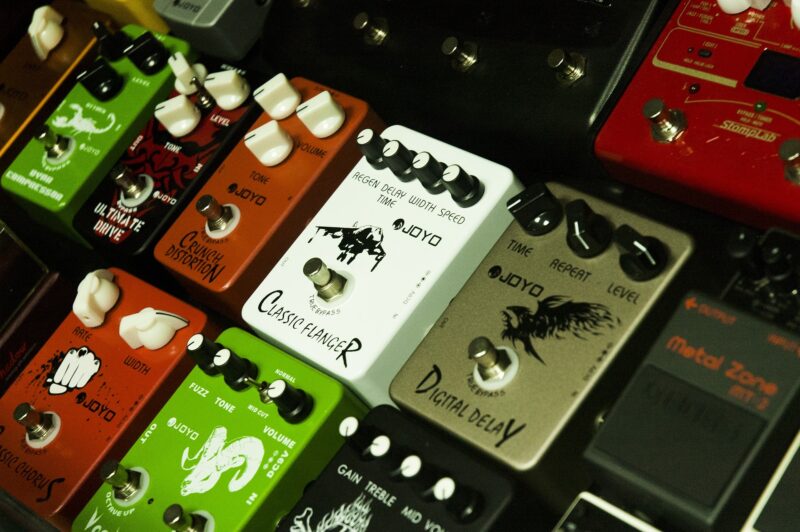
The world of guitar pedals has come a long way since the first fuzzes were built. It used to be that only electrical engineers had the know how, resources, and experience to build guitar pedals. Fortunately, a lot of that has changed.
Many of the secrets to great-sounding pedal builds are available online, and the tools and parts needed to build them are readily available. The only thing stopping you is figuring out where to get started. Here is how to start your first guitar pedal building project.
1.) Decide What You Want To Build
The first step in any project is deciding what you want to build. There are plenty of guitar pedal circuit types to choose from.
Start by thinking about the sound that you want. Do you prefer the sound of a fuzz over an overdrive? Would you rather have spring reverb over hall reverb? It all depends on what you like and what you want to create.
When choosing a circuit for your first build, it is a good idea to start with a boost or a fuzz curcuit. The reason why many experienced builders suggest these two options is because they can be made with fewer than ten components, don’t require circuit boards, and have some of the simplest designs available.
If you are new to guitar pedal building, start with a very basic fuzz like the one found in the early fuzz face designs. At this point, you are just trying to build familiarity with the process, so picking a hard circuit may just lead to frustration.
2.) Research the Circuit Online
Once you have decided what circuit you want to build, research the circuit online. You can find a vast number of guitar pedal circuits online. In fact, you can likely find a basic version of nearly any circuit that you want to build freely available.
This is largely because most of the popular circuits have been analyzed and re-engineered for years. On top of that, it is next to impossible to copyright or trademark the circuitry in electronic devices like guitar pedals since they are all made of common, non-proprietary parts.
There is a debate that still continues to this day whether it is okay to copy these circuits. The short answer is yes, it is okay to copy the circuit itself. That’s how many people learn and grow as builders and engineers. However, it is not okay (or legal) to copy a finished product.
Put simply, you can copy the circuit, but not the finished pedal if you plan to sell them. You will need to create your own artwork for the enclosure and brand it as something other than what the original circuit was used for. You also cannot sell copies of the schematics for the original. You have to make your own drawings if that’s something that you want to do, as well.
3.) Collect the Parts and Tools
As you move closer to starting your first build, you’ll need to acquire all of the materials that you need. This can be a bit of a daunting, and more expensive, task for your first build since you’ll need specific equipment and parts.
There are two types of things that you’ll need to acquire: equipment and parts. here is a short breakdown of what you’ll need for each. For a more in-depth list and recommendations, check out our post on Guitar Pedal Building Supplies.
Guitar Pedal Building Equipment
The best place to start is by acquiring your equipment. These are things that you need like tools and supplies so that you can build. While parts are generally used up on each project, most of your equipment is reusable and you may only have to buy it once. Here are a few things that you definitely need:
- Soldering iron and solder
- Fume extractor (like a reverse fan that pulls smoke away from your face)
- heat-resistant silicone mat
- Helping hands or circuit board holder if you need extra hands
- Breadboard for prototyping
- Circuit boards for the final build
- Enclosure to put the final build in
There are plenty of other things that you could use to build your pedals. For example, an oscilloscope, multi-meter, and variable power source can be very helpful. However, these are things that you don’t need. Once you settle into a building routine and get more experience, you’ll add to your toolkit to make building easier and giver yourself more options. For now, just focus on the essentials so that you can get started.
4.) Breadboard Everything
When you begin assembling your first guitar pedal circuit, the best way to do it is to use a breadboard. Breadboards are designed specifically for prototyping electronic circuits before you have to solder or modify parts. It gives you the chance to test things without making permanent connections so that you can experiment and know that what you made works before putting it together.
No matter how good of a builder you are, you should take the time to breadboard every new design. This is especially true if you are using parts that are expensive or hard to find. Nothing kills your desire to build like finishing a build and discovering that the rare reverb circuit that you were able to salvage actually doesn’t work.
Breadboarding is about more than just pre-testing your circuits. It gives you the chance to explore new options. Many of the pedals that you see on the market today are variations of older designs. Builders just like you wanted to creating something similar, but distinctly different from their favorite pedals. Building it on a breadboard gave them the chance to replace components and tweak designs until they created something new.
5.) Design Your Enclosure
When you have a functioning circuit on your breadboard that you want to turn into a finished product, its time to start thinking about what that final product will be. You have to consider two things: the enclosure and the circuit board. Essentially, you start to design the outside and the inside of the pedal.
The enclosure is the easiest place to start. It can also be the most fun to work on. You need three things in every enclosure design:
Labels
The labels show the user what the controls do. Make sure that the labels are easy to read against the background design. Without good labeling, it can be difficult to use a new pedal.
If you are only building the pedal for yourself, then you can skip the labels. However, you may want to include labels, or at least include an instruction manual, if you are sending the pedal to someone else.
Artwork
Perhaps the most enjoyable part of designing your enclosure is the artwork. Your artwork should help your pedal stand out from any other. In essence, it is the branding of your pedal.
In reality, you don’t have to include any artwork on your pedals. There are many designers that go with a bare aluminum case design and thoroughly enjoy it. However, consider what you are building pedals for. It is much harder to sell pedals without artwork since it is the artwork that initially gets buyer’s attention.
Branding
If you are planning on selling or producing multiple copies of a pedal, include some type of branding on it. Ideally, your branding will include the name of the company or designer, a logo, and a name for the pedal. However, you can get away with a just a simple logo. If you make more than one pedal design, you need to include a name so that people can tell them apart.
6.) Draw Your Circuitboard
The next step focuses on turning your circuit design into a finalized circuit board. There are many ways to do this depending on how you started the initial design. You could put your design into one of the many circuit design programs available, which can convert a circuit diagram into a circuit board map. If you are good with computers, this is the easiest way.
Alternatively, you can buy perfboard (waifer boards with holes in them) and create the final design yourself. The holes are laid out in a grid pattern and you just have to find the best way to get all of the parts to fit. This is where many people start with their early builds since you don’t need to know how a computer program works.
The best part about using perfboard is that you can put the pieces on the board without creating permanent connections right away. Just stick the legs of each piece through and bend them so that it sticks. When you are ready, solder them together according to your design and clip the excess.
In some cases, you can even skip the circuit board entirely. If your parts are long enough and rigid enough, you can solder them to each other without a board and fit everything within the enclosure. This will only work for simpler designs that can work with point-to-point soldering, like a simple fuzz circuit or a booster.
Whichever option you choose, get a few extra parts before you start. That way, you have extras if you mess up and damage one of the parts. This is especially important if you are new to soldering.
7.) Solder Everything Together Testing For Continuity
The next step is often the hardest part and where you may experience the most problems. Once you have a finished circuitboard design, you can start to solder on the parts. Keep in mind the layering of your parts. If you have parts that are shorter, like opamps or resistors, put them on the board first. That way, you don’t have to bend parts out of the way to place them.
In fact, you want to avoid bending parts once they are soldered if possible. Bending them can break connections or wear out the legs on those parts.
8.) Drill and Put It In the Enclosure
With a finished circuitboard, you know exactly where all of the parts that need to stick out of the enclosure go. Take your measurements and mark your enclosure for drilling. If you are having trouble telling exactly where the holes should go, try separating knobs, jacks, and LEDs from your board. Instead, attach them using wires so that they can be moved to where you need to put the holes.
Drilling holes in your enclosure is best done with a drill press and a step bit, although you can do it with a hand drill. Just be careful when using a hand drill as the torque can hurt your hand and wrist if the bit gets stuck.
9.) Decorate Your Enclosure
Once the board is done, do the work on your enclosure. Decorating enclosures can be a lot of fun, and there are a lot of options at your disposal. There really is no right or wrong way, but there are specific advantages to different methods.
UV Printing
UV printing is the industry standard for professionally-made pedals. A special UV printer that is designed to handle printing surfaces like pedal enclosures spray UV-sensitive ink onto the surface. The ink dries almost instantly due to a UV light located next to the spray head on the printer.
Not only is UV printing more accurate than other methods, the ink is also more durable. UV-sensitive ink is very hard to remove once it is applied and dried. You also get the creative freedom of printing nearly anything on your enclosure. UV printers are as accurate as other printers since they are, essentially, regular printers that can handle larger things to print on than paper.
The downside to UV printing is that the machines are expensive, and you may not want to own one of them yourself. Aside from the high cost, they require a lot of space and maintenance. if you are just starting out, your best option is to find someone that will do the printing for you. There are companies that can run batches of pedals for you if you are planning on selling a significant number of pedals. Alternatively, there are some printers who will run small or even single batches for you.
Screen Printing
Another tried and true option is screen printing. It involves making a template out of silk screen and using it to paint your enclosures similar to how t-shirt manufacturers print on their t-shirts.
The biggest benefit to screen printing is that you do not need complex machinery to do it. In fact, you could get by with a silk screen, enamel paint, and a squeegee. The actual setup that you would use is a bit more complicated than that, but you could do it with just those three things.
The downside to screen printing is that you have to make your own silk screens, which can be a bit complicated, unless you can find someone to do it for you. Fortunately, a local printing shop may be able to help you with this.
10.) Assemble, Test, and Adjust
Finally, you are most of the way through the project and you get to do the part that most builders dream about. Its time to assemble the final product and test it. If you can get everything into your enclosure, close it, and it works, you’ve done it! You made your first pedal.
The very next thing you should do is test it. There are plenty of ways to test a new pedal, but the simplest way is to just plug in and play. Its important that you do this for every pedal that you make since it is half of the fun of doing this in the first place. However, it is also a good business practice if you plan on selling your creations. You need to know if your finished product is safe and good quality. Most of the time, the only way to really know is to spend time with it in a practice room.
Don’t be surprised if it does not sound exactly like you wanted it to. Small changes can lead to significant differences in the finished product. It is never too late to go back in change a component or two to make a few adjustments. Since its your creation, you can go back and adjust as much as you want until you get it just right.
Be Safe and Have Fun
There it is in a nutshell, the process for finishing your first pedal from scratch. When you set out on this project, always remember two things: be safe and have fun.
Pedal builders don’t get into this because they are want the money or they want to be famous. You could buy a lot of the pedals that you’ll build for less and there are better pathways to fame. They get into this because if is fun. Take the time to make sure that you are enjoying the process as you go through it. There will be difficulties, but you can always find a way around them. Don’t let this become another source of stress in your life.
You can reduce a lot of the stress in pedal building by learning to do things safely. Soldering, circuit designing, and manufacturing can be difficult and dangerous if you don’t understand basic safety procedures. Before you set out on any project, make sure that you have the right safety equipment and understand the risks. You’ll feel a lot better about what you are doing if you are not as worried about doing it safely.
Learn More About Guitar Pedal Building from BGL
Here at Builder’s Guitar Lab, our goal is to show you what its like to build guitar pedals and some other guitar gear on your own. We are not experts in this by any means, but we can promise you a deep look into the projects that we work on and some entertaining content along the way. That way, you can see what its like, learn a few things, and have a fun time building your own gear.
Learn more about guitar pedal building on the BGL blog.